النبات
مواضيع عامة في علم النبات
الجذور - السيقان - الأوراق
النباتات الوعائية واللاوعائية
البذور (مغطاة البذور - عاريات البذور)
الطحالب
النباتات الطبية
الحيوان
مواضيع عامة في علم الحيوان
علم التشريح
التنوع الإحيائي
البايلوجيا الخلوية
الأحياء المجهرية
البكتيريا
الفطريات
الطفيليات
الفايروسات
علم الأمراض
الاورام
الامراض الوراثية
الامراض المناعية
الامراض المدارية
اضطرابات الدورة الدموية
مواضيع عامة في علم الامراض
الحشرات
التقانة الإحيائية
مواضيع عامة في التقانة الإحيائية
التقنية الحيوية المكروبية
التقنية الحيوية والميكروبات
الفعاليات الحيوية
وراثة الاحياء المجهرية
تصنيف الاحياء المجهرية
الاحياء المجهرية في الطبيعة
أيض الاجهاد
التقنية الحيوية والبيئة
التقنية الحيوية والطب
التقنية الحيوية والزراعة
التقنية الحيوية والصناعة
التقنية الحيوية والطاقة
البحار والطحالب الصغيرة
عزل البروتين
هندسة الجينات
التقنية الحياتية النانوية
مفاهيم التقنية الحيوية النانوية
التراكيب النانوية والمجاهر المستخدمة في رؤيتها
تصنيع وتخليق المواد النانوية
تطبيقات التقنية النانوية والحيوية النانوية
الرقائق والمتحسسات الحيوية
المصفوفات المجهرية وحاسوب الدنا
اللقاحات
البيئة والتلوث
علم الأجنة
اعضاء التكاثر وتشكل الاعراس
الاخصاب
التشطر
العصيبة وتشكل الجسيدات
تشكل اللواحق الجنينية
تكون المعيدة وظهور الطبقات الجنينية
مقدمة لعلم الاجنة
الأحياء الجزيئي
مواضيع عامة في الاحياء الجزيئي
علم وظائف الأعضاء
الغدد
مواضيع عامة في الغدد
الغدد الصم و هرموناتها
الجسم تحت السريري
الغدة النخامية
الغدة الكظرية
الغدة التناسلية
الغدة الدرقية والجار الدرقية
الغدة البنكرياسية
الغدة الصنوبرية
مواضيع عامة في علم وظائف الاعضاء
الخلية الحيوانية
الجهاز العصبي
أعضاء الحس
الجهاز العضلي
السوائل الجسمية
الجهاز الدوري والليمف
الجهاز التنفسي
الجهاز الهضمي
الجهاز البولي
المضادات الحيوية
مواضيع عامة في المضادات الحيوية
مضادات البكتيريا
مضادات الفطريات
مضادات الطفيليات
مضادات الفايروسات
علم الخلية
الوراثة
الأحياء العامة
المناعة
التحليلات المرضية
الكيمياء الحيوية
مواضيع متنوعة أخرى
الانزيمات
Materials for the Manufacture of Microfluidic Components
المؤلف:
Prof. Dr. Christof M. Niemeyer, Prof. Dr. Chad A. Mirkin
المصدر:
Nanobiotechnology: Concepts, Applications and Perspectives
الجزء والصفحة:
p19-21
2025-01-25
421
Three types of materials are common for microfluidic and Lab-on-a-Chip devices: silicon, glass, and polymer materials.
Silicon
Silicon is the dominant material in microelectronics, and knowledge of micromachining of this material has been accumulated for several decades. Because of this, silicon has also been the dominant material used in nonelectronic applications of MEMS and, in the past, also in microfluidics. In fact, the known micromachining methods for silicon are well suited for the generation of high-precision fluidic structures. For example, channels with square or V-shaped cross-sections can be easily generated.
Among the advantages of silicon are the simple generation of an inert surface (SiO2)by oxidation, high-temperature stability, high chemical resistance to organic solvents and acids, well-established bonding processes, an extensive knowledge about coatings, and its well-defined and excellent mechanical properties as a single crystal material.
Silicon may be the material of choice if electric functions such as heaters and sensors are required as part of the microfluidic component. These can be easily integrated into the silicon substrate using standard microelectronics fabrication technology.
The disadvantages of silicon are the nonideal surface for many biochemical applications , and the high price for material and processing. Silicon is a relatively expensive, single-crystal material, and the process equipment, process materials from microchip technology are very expensive. As fluid chips tend to be much larger than electronic chips, this may lead to high manufacturing costs per chip. Another cost disadvantage is that the batch processing sequence used for silicon is more complicated than the one-step re plication methods used for polymers. In the silicon process, the alignment of subsequent layers must be carried out for each wafer in production. In polymer replication technology, the alignment is necessary only during the production of the master, eliminating this error source once the master has been correctly manufactured.
Furthermore, silicon cannot be used for applications involving electrical fields (e.g., capillary electrophoresis) due to its low electrical resistance.
FIG1. Capillary electrophoresis chip for nucleic acid separation. (Courtesy Caliper Technologies, Inc.)
Glass
Glass is another important material for the production of microfluidic components and systems; borosilicate types of glass are often used. Some of these glasses, such as Boro float or Pyrex 7740, have thermal expansion coefficients which are matched to that of silicon, and are used together with silicon in stacked arrangements, for example as trans parent cover plates. These glasses can be bonded to silicon by anodic bonding, without the need of a bonding material. The advantages of glass are its high chemical resistance, excellent thermal and mechanical stability, and optical transparency. In many cases, glass is well-suited as a surface for biological and chemical reactions. There is an extensive knowledge about inorganic and organic coatings with glass as a base material. Auxiliary electric functions (e.g., heaters) may be added using the well-established procedures of thin film technology. Glass is also well-suited for electroosmotic flow applications and capillary electrophoresis [1]. An example is shown in Figure 1.
Although glass as a base material is less expensive than silicon, batch fabrication, optical polishing steps, and the micropatterning steps will lead to comparatively high production costs. Micromachining procedures for glass are much less developed than for silicon, and in most cases isotropic etching is used. High-aspect ratio and multilevel structures are difficult to manufacture, and this restricts the use of glass to simple applications such as array chips, single depth channel networks (e.g., capillary channels), or intermediate and cover plates in stacked arrangements.
The photostructurable glass FOTURAN (Schott) allows the fabrication of high-aspect ratio fluidic structures, but the disadvantages are high substrate and processing costs, and compared to other materials a high surface roughness of the structures.
Polymers
Polymers are the third type of material used in the manufacture of microfluidic devices [2]. The main benefit of polymer materials is based on simple and cost-effective replication methods such as injection molding or hot embossing, because this allows the manufacture of all microstructures of the device in one manufacturing cycle. The capabilities of these manufacturing processes in the micro and nano regime are illustrated by the manufacturing of CDs and DVDs, where a 120 mm-sized device, including metallization and printing, can be manufactured for much less than 1$– dramatically less than for a silicon or glass device of the same size. However, these replication methods require the manufacture of a master structure, which is used as a tool in the replication step. As the manufacturing cost of the mastering is considerable, these methods only make sense for high-volume applications, where at least a few 100000 parts are manufactured, and the mastering cost can be shared by many replicated parts.
Another advantage of polymers is the broad range of materials suited for these manufacturing methods, including PMMA, PS, PC, cyclic olefins, PEEK, POM, elastomers, and others. This allows a choice to be made of the material properties suitable for the specific application. Typical properties of the material that may be of fundamental importance include optical transparency, autofluorescence, thermal expansion coefficients, and stiffness. A summary of the properties for a range of materials is provided in Ref. [2].
Convenient sealing methods, such as lamination, ultrasonic welding, laser welding, gluing or thermal bonding, are available for polymer devices.
One disadvantage of polymer materials is a reduced thermal stability, as these devices can only be operated at temperatures below the glass transition temperature. This also limits processes to coat or functionalize the polymer surface. Another disadvantage is the reduced stability against organic solvents, acids, and bases.
A variety of methods for chemically modifying the plastic surface, and functionalizing the surface have been published, and extensive work is under way in that field. Most polymer surfaces are not hydrophilic with respect to the fluids used in nanobiotechnology, and will require a suitable surface modification (e.g., plasma polymerization) if capillary forces are to be used for fluid transport.
References
------------
[1] B. Heymann, H. Grubmüller, Phys. Rev. Lett. 2000, 84, 6126–6129.
[ 2 ] D. Bartolo, I. Derény, A. Ajdari, Phys. Rev. E 2002, 65, 051910.
الاكثر قراءة في التراكيب النانوية والمجاهر المستخدمة في رؤيتها
اخر الاخبار
اخبار العتبة العباسية المقدسة
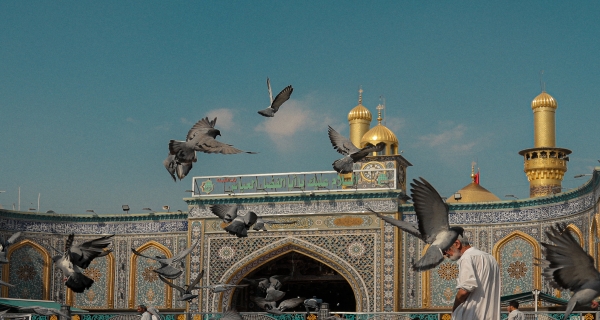
الآخبار الصحية
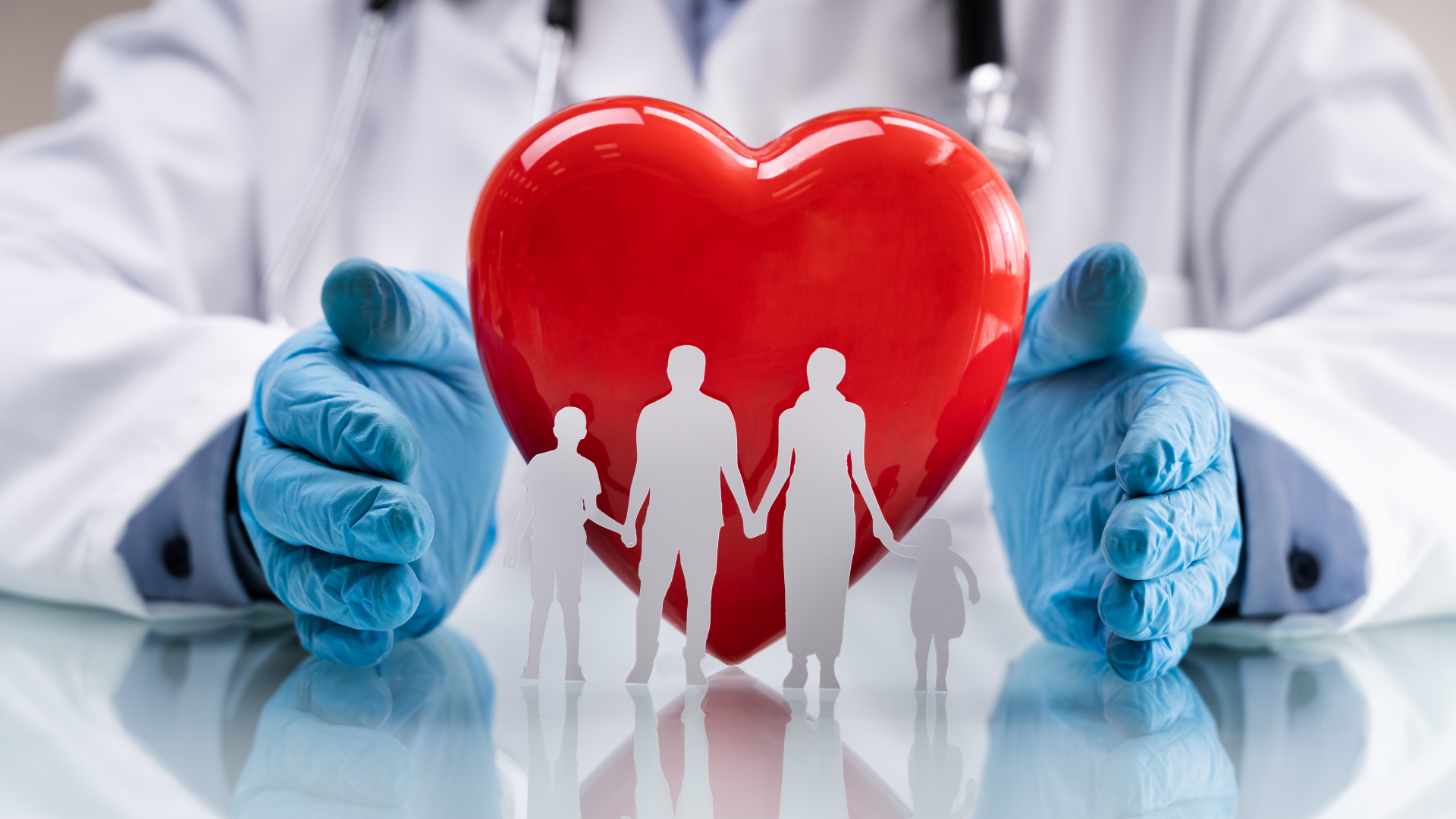